Last Revised: October 19, 2023
Issued 4/2019, Reviewed 1/2022 (KB)
The following SOP covers the hazards and controls for working with glassware under vacuum.
Some of the material in this SOP was derived from the Dow Safety Academy video course, Vacuum Equipment. Time stamps for the content in the video are shown in parentheses with the corresponding information below.
Hazard Description
Vacuum systems remove gas from an enclosed vessel or space, creating negative pressure inside, which results in higher pressure outside. Thus, any container under vacuum must be regarded as an implosion hazard (1:17). Evacuated glass vessels may collapse violently, either spontaneously, from strain, or from an accidental blow. Implosions can result in flying glass, spattering chemicals, and fire.
There are many laboratory applications for vacuum systems. This SOP is generic and applies to typical uses of vacuum in the lab such as glassware under house vacuum or high-vacuum (oil diffusion or belt-driven pumps).
Certain high-hazard tasks or equipment will require a written Hazard Control Plan (HCP) to manage the risks or to account for factors not addressed in this SOP. For example, the risks of ultra-high-vacuum chambers, cryo-pumping reactive materials, or vacuum evaporation applications for nanomaterials, are not covered by this SOP and require a written HCP. The PI of the lab must assess the risks of the lab tasks and equipment to determine whether an HCP must be developed. Contact EHRS if you are unsure whether an HCP is needed.
Assembling Vacuum Apparatus
Consider the following when setting-up a vacuum apparatus (2:00):
- Locate the equipment in an area where the evacuated vessel will not be bumped or disturbed.
- Vent pump into a dedicated local exhaust duct, or if local exhaust is not available, into a fume hood.
- Assemble equipment to avoid strain on tubing and connections. Various sections of the system should be able to be disconnected without transferring strain to the necks of the flasks.
- Support heavy apparatus from below (for example, with a lab jack and cork ring), as well as by the neck (for example, with a clamp).
- Locate the apparatus in a fume hood or behind a suitable shield (see “Glassware Shielding and Containment” section below).
Glassware Selection
Use only glassware that is designed for use in vacuum operations (2:40). Do not use flat-bottomed flasks or glass vessels with angled or squared edges in vacuum applications unless specifically designed for the purposes (e.g. heavy-walled filter flasks).
Inspect glass for flaws before use. Do this every time you use a piece of glassware under vacuum, and do not use the item if there are any star cracks, scratches, or etching. These flaws can often be noticed best if the vessel is held up to light.
Hand-blown glassware should not be subjected to vacuum unless it has been appropriately annealed. Repaired glassware must be properly annealed and inspected with a cross-polarizer before vacuum or thermal stress is applied.
Glassware Shielding and Containment
During vacuum operations, the system must be shielded at all times. All glass vessels under vacuum must be considered to be implosion hazards. Use the hood sash, a portable blast shield, or other shielding device designed to contain the force of flying glass that would be expelled by an implosion event (5:00).
Securely clamp all vessels including the sample flask and the receiving flask, as well as the traps.
Place a secondary container under any liquid-containing flask that is under vacuum. This will help contain spills in case of equipment failure.
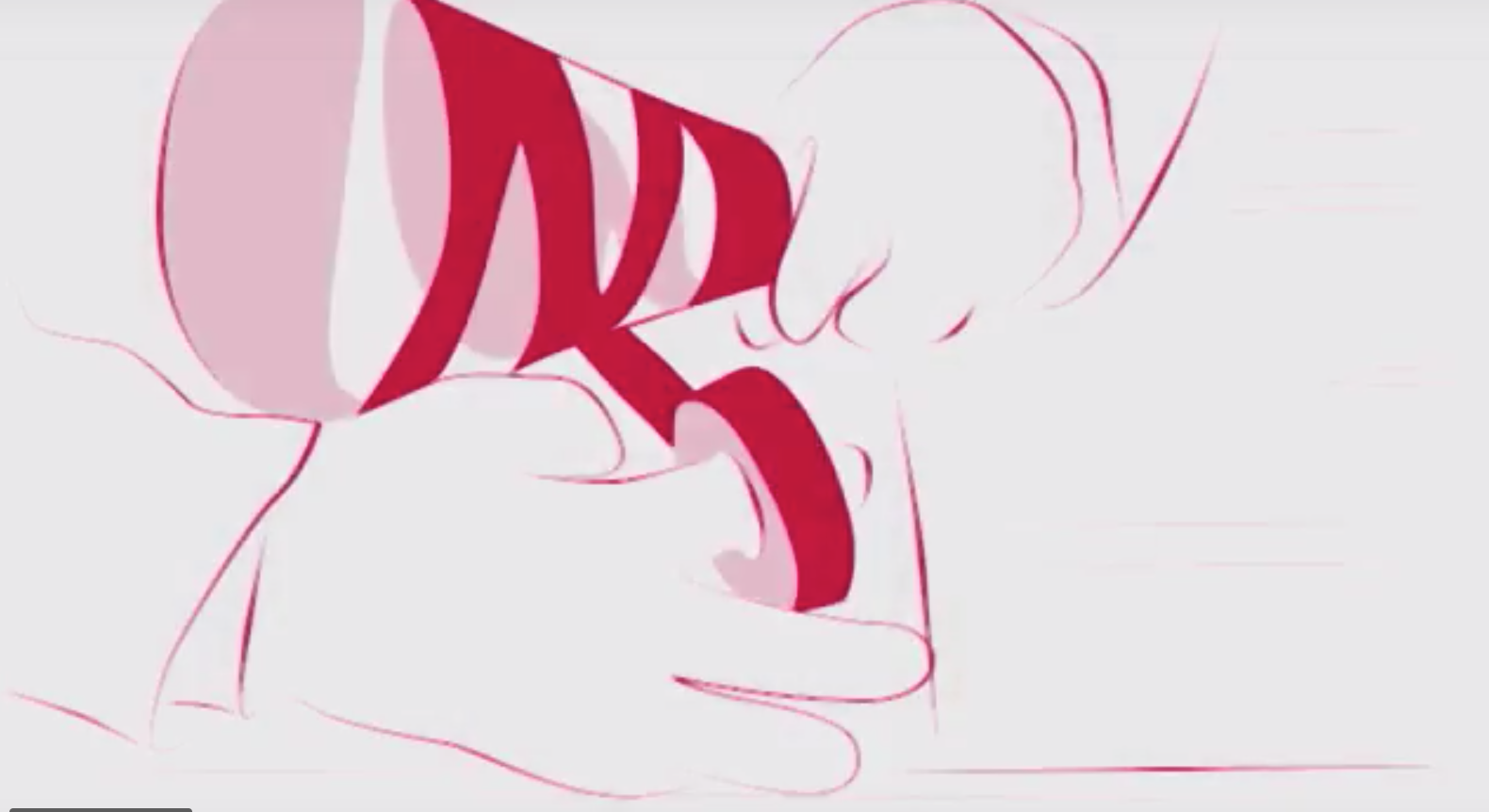
Some glassware designed for vacuum use is coated in a resin (plastic) to contain implosion. If the glassware is not coated, it can be wrapped in fiber-reinforced friction tape in a grid pattern to help contain glass in case of implosion (3:20).
Another method of containing glass is the use of poly netting. Tape, netting, or plastic coating must also be used around evacuated dewar flasks that are under permanent vacuum.
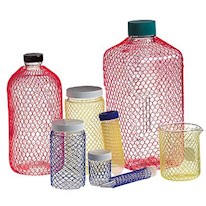
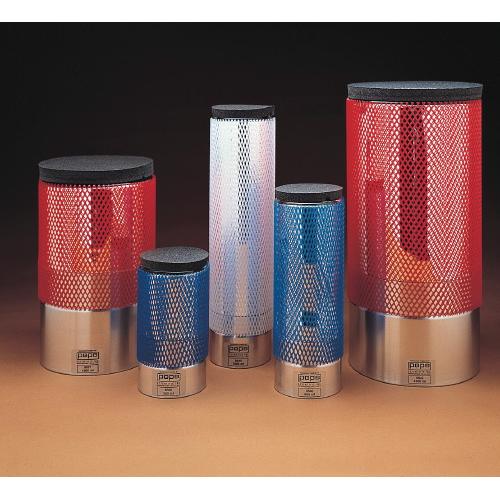
Cold Traps and Venting
Additional information about cold traps and venting can be found in the following sections Penn’s CHP: SOP: Cryogens and Dry Ice and Fact Sheet: Vacuum Pump Use and Installation.
Cold traps are used to condense vapors evaporated from evacuated vessels. The cold trap is important to protecting both stand-alone vacuum pumps and house vacuum systems.
Consider the following when selecting a cold trap:
- Size: How much liquid do you expect to condense?
- Temperature: How cold must the trap be to condense the vapor of a given material at the vacuum level you are using?
- Coolant: Take into account whether there are any flammability or frothing issues that must be considered for this operation.
- See SOP: Cryogens and Dry Ice for important information about the risk of condensing liquid oxygen in cryogen-cooled traps.
Other Specialized Vacuum Equipment
The following was adapted from: National Research Council (US) Committee on Prudent Practices in the Laboratory. Prudent Practices in the Laboratory: Handling and Management of Chemical Hazards: Updated Version. Washington (DC): National Academies Press (US); 2011. 7, Working with Laboratory Equipment. Available from: https://www.ncbi.nlm.nih.gov/books/NBK55884/
Vacuum manifold/Schlenk Lines
Vacuum lines must be contained in a fume hood or in another shielded enclosure. High-vacuum manifolds on the open bench are not permitted. Protect vacuum and Schlenk lines from over pressurization by using a bubbler. If a slight positive pressure is desired, the recommended pressure range must not be in excess of 1 to 2 psi, which can be obtained by adjusting the depth of the exit tubing in the bubbler liquid.
Desiccators
Use solid desiccants instead of vacuum whenever possible. Glass desiccators must be constructed of Pyrex (borosilicate) glass and must be completely enclosed in a shield or wrapped with friction tape in a grid pattern that leaves the contents visible. Although plastic desiccators reduce the risk of implosion, they should also be shielded while evacuated. Never carry or move an evacuated desiccator. Cracked or chipped desiccators must never be subjected to vacuum.
Rotary Evaporators
Rotary evaporators (rotovaps) must be shielded to protect operators from risk of glassware implosion. When a rotovap is not contained in a fume hood or similar enclosure, the glass components must be plastic-coated or wrapped in friction tape or poly netting to contain glass in case of implosion. When operating the rotovap, gradually increase rotation speed and application of vacuum to the sample flask. Take care to avoid bumping the flask on the bottom or edge of the water bath.
Related SOPs and Fact Sheets
References
- Dow Safety Academy, Specialized Topics Video, Vacuum Equipment. https://corporate.dow.com/en-us/science-and-sustainability/lab-safety/specialized-topics
- National Research Council (US) Committee on Prudent Practices in the Laboratory. Prudent Practices in the Laboratory: Handling and Management of Chemical Hazards: Updated Version. Washington (DC): National Academies Press (US); 2011. 7, Working with Laboratory Equipment. Available from: https://www.ncbi.nlm.nih.gov/books/NBK55884/