Last Revised: November 14, 2024
Biosafety Cabinets (BSCs) are designed to provide three basic types of protection:
- Personnel protection from harmful agents inside the cabinet
- Product protection to avoid contamination of the work, experiment or process inside the cabinet
- Environmental protection from contaminants contained within the cabinet
If you are looking to purchase a new biosafety cabinet, need help selecting the type of cabinet or the location for the biosafety cabinet, contact EHRS at 215-898-4453 and ask to speak to a biosafety officer.
Biosafety Cabinet (BSC) FAQ
How often should my BSC be certified? Biosafety cabinets must be certified annually, when new after installation, when moved to a new location, and after a significant service to the equipment.
How do I get my BSC certified? BSC must be certified annually by a third party vendor with NSF 49 accreditation. For BSCs in Penn-owned buildings, Technical Safety Services (TSS), Inc. is Penn’s designated biosafety cabinet service for BSC certifications (required annually). Annual certification by TSS is done by building on a set schedule. However, if your BSC is new or was not certified during the regularly scheduled certification, please contact TSS to schedule a certification (upenn@techsafety.com).
Who pays for BSC certification? Annual certifications for BSCs in Penn-owned buildings are covered by a purchase order by FRES only if the certification is conducted during the regularly scheduled certification period. TSS will still reach out to the lab’s PI and Lab Safety Coordinator to notify them of the upcoming scheduled certification. BSC certifications that are completed outside of the regularly scheduled certification period, such is the case with new BSC certification, may be charged to the BSC owner. In non-Penn owned buildings, BSC certification fee is paid for by the BSC owner.
How do I get rid of an old BSC? Prior to disposal, the BSC must be professionally decontaminated. Contact Technical Safety Services (TSS), Inc. to schedule the decontamination (upenn@techsafety.com). Work with your building administrator to coordinate the disposal of the decontaminated BSC through eForce Recycling (https://www.eforcecompliance.com/) or Elemental Recycling (http://eleminc.com/). After the BSC is discarded, email biosafety@lists.upenn.edu to remove the BSC from your lab's BioRAFT Equipment Module.
How old is too old for a BSC? The expected lifespan for a BSC is 15 years. Beyond that age, manufacturers stop supporting equipment in favor of newer technologies. In addition, finding parts for older BSCs may become impossible or prohibitively expensive. See the Aging Biosafety Cabinets section for more information.
Do I have to get my BSC certified if I haven't used it in a while? Your BSC must be certified annually even if it is not used often. This is to verify that the BSC meets the performance standards.
How do I get a new BSC? BSCs may be purchased from several reputable manufacturers, including NuAire and Baker (preferred). If you are looking to purchase a new biosafety cabinet, need help selecting the type of cabinet or input for a proper location for the biosafety cabinet, contact EHRS at 215-898-4453 and ask to be directed to a biosafety officer.
My lab just received a new BSC. What do I need to do next? All new BSCs must be certified after installation and before use. Please contact Technical Safety Services (TSS), Inc. (upenn@techsafety.com) to schedule the certification.
How can I replace the UV light in my BSC? Installation of UV light in a BSC is generally not recommended because it is ineffective as a primary decontamination method (please see the section on UV Lights and Biosafety Cabinets below for further information). If a UV lamp replacement is required, Technical Safety Services (TSS), Inc. can offer this service. Please contact TSS (upenn@techsafety.com) to schedule the service.
Can I complete required maintenance in my own BSC? Maintenance done by untrained and unaccredited personnel will void certifications and warranties associated with the BSC. All maintenance on your BSC must be completed by an NSF accredited technician. Contact TSS (upenn@techsafety.com) for any maintenance issues or concerns.
How far can I move my BSC before I must recertify it? A BSC must be recertified if it is moved, even when the move is within the same room. Contact TSS (upenn@techsafety.com) to schedule a certification if you have moved or need to move your BSC.
Which disinfectants can I used in my BSC? Always use the most appropriate disinfectant for the pathogen or organism handled in the BSC. Some disinfectants, such as 10% dilution of household bleach, can be corrosive on the stainless steel surface of your BSC. When using 10% dilution of bleach to decontaminate the BSC, allow sufficient contact time and follow with a wipe using 70% ethanol or sterile water to remove residual bleach. For more information, please refer to the section on BSC Disinfection & Chemical Compatibility below.
My BSC is making weird noises. What should I do? Discontinue use of the BSC immediately if you detect an issue with your BSC. Post a sign on the sash of the BSC to let others know of the issue. Contact TSS (upenn@techsafety.com) to schedule an appointment to troubleshoot the problem.
BSC Certification & Repair
Biosafety cabinets must be certified annually by a third party vendor with technicians accredited under NSF/ANSI Standard 49. Technical Safety Services (TSS) is a BSC vendor available on campus that provides certification and repair services. TSS has been vetted and approved by Penn purchasing and a competitive pricing contract is in place with the company.
A third party vendor must be contacted under the following circumstances:
- If you have a new cabinet requiring certification
- A cabinet that has been moved requiring certification
- A cabinet in need of troubleshooting, repairs, or decontamination
To request service with TSS:
-
Email: upenn@techsafety.com
TSS can be found in Ben Buys under Technical Safety Services
Instructions for preparing your biosafety cabinet for certification/repair
Aging Biosafety Cabinets
The lifespan of a biosafety cabinet is 15 years. Beyond that, manufacturer support and parts availability may be limited. This may result in costly repairs, long wait times for parts and repairs, or the biosafety cabinet not being repaired. Due to improvements in ergonomics, safety containment performance, energy efficiency, and serviceability, biosafety cabinets manufactured before 2000 are considered obsolete. Labs may continue to use these biosafety cabinets if they pass an annual certification. All repairs and certifications must be completed by NSF accredited technicians. Absolutely no “in-house” parts or repairs are permitted.
The following Baker Biosafety Cabinets are no longer supported by the manufacturer:
VBM |
SC-4TX |
SC-6TX |
SG250 |
SG400 |
SG600 |
B40A |
B315 |
B4000 |
B6000 |
B40 |
B60 |
B40A |
B60A |
B40-112 |
B60-112 |
B40A-112 |
B60A-112 |
B40A |
4TX |
6TX |
BC-4 |
BC-6 |
NCB4 |
NCB6 |
NCB-B |
NCB-C |
CVF |
UVF |
|
While outdated, the Baker Company will endeavor to support the following SterilGARD models, as long as parts are available:
- SG403 & SG603
- GS403A &SG603A
NuAire may provide limited support to biosafety cabinets older than 15 years.
See the technical bulletins from Baker and NuAire.
1.0 Purpose and Applicability
- 1.1 This policy is designed to ensure biosafety cabinets used at the University of Pennsylvania by university employees and students are certified and repaired to NSF/ANSI Standard 49.
- 1.2 This policy is also designed to outline the expectations for biosafety cabinet lifespan and retirement.
- 1.3 The policy applies to all biosafety cabinets used and stored across Penn’s campuses.
2.0 Definitions
- 2.1 “Biosafety cabinets” (BSC) are a type of biocontainment equipment used in biological laboratories to provide personnel, environmental, and product protection.
- 2.2 “NSF/ANSI” refers to a set of standards developed to promote public health, safety, sustainability assessment, and the environment. The National Sanitation Foundation (NSF) is an independent organization that develops standards and conducts product testing, inspection, and certification. The American National Standard Institution (ANSI) is a US-based non-profit organization that manages the development of voluntary consensus standards for products, services, techniques, systems, and personnel. Together, these organizations develop many standards followed by the University of Pennsylvania.
- 2.3 “NSF/ANSI Standard 49” is the standard that outlines basic requirements for design, construction, and performance of BSCs. The standard provides personnel, product, and environmental protection and ensures the reliable operation, durability, and safety of BSCs. The standard also includes detailed test procedures and informational annexes, including recommendations for installation, field certification tests, and decontamination procedures.
- 2.4 “NSF Accredited Biosafety Cabinet Field Certifiers” (NSF Accredited Technicians) are individuals who have achieved accreditation from the NSF to perform field certifications of biosafety cabinets to the NSF/ANSI Standard 49. They are also trained to make repairs to and chemically decontaminate biosafety cabinets.
3.0 Roles and Responsibilities
3.1 The Office of Environmental Health and Radiation Safety (EHRS) is responsible for:
- 3.1.1 Providing guidance to university employees on the use, purchase, placement, and replacement of biosafety cabinets.
- 3.1.2 Communicating with NSF Accredited Technicians any specific needs of university employees or campus research organizations
- 3.1.3 Inventorying biosafety cabinets across Penn’s campuses.
3.2 University Research Faculty & ULAR are responsible for:
- 3.2.1 Purchasing biosafety cabinet(s), providing adequate facilities for the biosafety cabinet(s), paying for the installation and the initial certification of the biosafety cabinets.
- 3.2.2 Paying for the annual certification of biosafety cabinets in Penn leased buildings.
- 3.2.3 Providing regular maintenance of the biosafety cabinet(s) in their possession, including, but not limited to HEPA filter replacements.
- 3.2.4 Scheduling and paying for biosafety cabinet repairs.
- 3.2.5 Scheduling and paying for professional decontamination of biosafety cabinet(s).
- 3.2.6 Scheduling and paying for removal and recycling of retired biosafety cabinet(s).
3.3 The Division of Facilities and Real Estate Services is responsible for:
- 3.3.1 Paying for one annual certification of any biosafety cabinet in Penn owned buildings as long as those biosafety cabinets are certified within the scheduled certification period (defined by the university’s biosafety cabinet certification schedule set by the preferred vendor).
4.0 Policies and Procedures
- 4.1 Biosafety cabinets must be certified at least annually by technicians accredited under NSF/ANSI Standard 49.
- 4.2 Biosafety cabinets can be serviced or repaired ONLY by individuals accredited under NSF/ANSI Standard 49 to certify and service biological safety cabinets.
- 4.3 Biosafety Cabinets at or beyond 15 years of service must be slated for replacement. Approval of funds or funding requests must be considered at this time.
- 4.4 Biosafety cabinets older than 15 years of service can be used and operated safely ONLY as long as they can be certified, or repaired and certified, to the NSF/ANSI 49 standard by an NSF/ANSI 49 accredited technician. As noted above, ONLY NSF/ANSI 49 accredited technicians or manufacturer’s representatives are allowed to repair biosafety cabinets.
- 4.5 Biosafety cabinets modified in any manner not sanctioned by the manufacturer, or ‘repaired’ by non-accredited individuals will have voided any applicable warranties and will be adjudicated ‘uncertifiable’. Such biosafety cabinets will be considered unsafe and unapproved for use and MUST be taken out of service, decontaminated, and removed from the laboratory.
- 4.6 Any biosafety cabinet older than 15 years of service which fails certification, cannot be repaired, or for which parts are no longer available must be taken out of service IMMEDIATELY, decontaminated, and removed from the laboratory.
5.0 References and Resources
- 5.1 Biosafety Cabinetry Certification: NSF/ANSI 49: https://www.nsf.org/lab-testing/biosafety-cabinetry/biosafety-cabinet-certification
NSF/ANSI 49 Annex 1 I-1.9 BSC lifespan The current lifespan of a BSC is approximately 15 years. Use of modern day BSCs began in the early 1970s with BSCs that were manufactured to the NIH-03-112C Standard and subsequently the NSF/ANSI 49. BSCs manufactured in the 1970s, 1980s, and early 1990s have provided over 15 years of service. Several considerations should be made of BSCs in this age group: — will the BSC need extensive service? (i.e., HEPA/ULPA filter replacement, blower / motor replacement, will the electrical wire harnesses need replacement, etc.); — can an older BSC be commissioned after it has been in storage or purchased as a resale? — will original test reports be available or will the BSC be commissioned to current NSF Standards? After 15 years, replacement parts may or may not be available due to electrical or mechanical changes at the factory or industrial part suppliers. For example, magnetic ballasts and T12 fluorescent bulbs may not be available. In addition, today's BSCs have evolved through the years with many improvements in containment, ergonomics, serviceability, and energy efficiency. That should be considered in a BSC repair versus replacement decision.
|
Prior to disposal, the BSC must be professionally decontaminated. Contact Technical Safety Services (TSS), Inc. to schedule the decontamination (upenn@techsafety.com). Work with your building administrator to coordinate the disposal of the decontaminated BSC through eForce Recycling (https://www.eforcecompliance.com/) or Elemental Recycling (http://eleminc.com/). After the BSC is discarded, email biosafety@lists.upenn.edu to remove the BSC from your lab's BioRAFT Equipment Module.
EHRS training is required for all those who will use a biological safety cabinet. Training is available in Workday Learning under the course title "Biosafety Cabinet Operation."
The following tutorial is a reminder for best practices within the BSC: Use of BSC Tutorial (pdf)
UV Lights in Biosafety Cabinets
The University of Pennsylvania does not require UV lights in biosafety cabinets. The Biosafety in Microbiological and Biomedical Laboratories, 5th Ed (Appendix A, Section VI), states the following:
Ultraviolet Lamps
“Ultraviolet (UV) lamps are not required in BSCs nor are they necessary. If installed, UV lamps must be cleaned weekly to remove any dust and dirt that may block the germicidal effectiveness of the ultraviolet light. The lamps should be checked weekly with a UV meter to ensure that the appropriate intensity of UV light is being emitted. UV lamps must be turned off when the room is occupied to protect eyes and skin from UV exposure, which can burn the cornea and cause skin cancer. If the cabinet has a sliding sash, close the sash when operating the UV lamp.”
For additional information, please read the following article:
Position Paper on the Use of UV Lights in BSCs [pdf]
The Office of EHRS at the University of Pennsylvania has taken a strong stance against the use of gas burners or alcohol flames in Biosafety Cabinets.
Biosafety Cabinets that are disconnected from existing gas supply during repair or relocation will not be reconnected.
This decision is in accordance with recommendations from numerous agencies. The Centers for Disease Control and Prevention (CDC) reports that “open-flames are not required in the near microbe-free environment of a biological safety cabinet” and create “turbulence which disrupts the pattern of air supplied to the work surface” jeopardizing the sterility of the work area. This is also the recommendation of the World Health Organization (WHO) as well as the major Biosafety cabinet manufacturers.
For more information on how heat sources impact airflow in the BSC, see the Baker Presentation on Heat in a BSC (pdf). Also watch these two Myth Busters Videos on heat in the BSC: Myth Busters - Heat in the BSC! and Heat in the BSC! (Myth Busters Supplement).
Solutions:
- Remove Bunsen burners and/or replace with alternative technology such as electric incinerators
- Use disposable loops, spreaders, and other instruments
- Autoclave instruments such as tweezers, scissors and scalpels
- If it is deemed absolutely necessary for the work being done, use a pilotless burner or touch-plate microburner to provide a flame on demand
Laminar Flow Clean Benches vs. Biosafety Cabinets
Clean Bench Information:
-
Horizontal laminar flow clean benches are NOT biosafety cabinets.
-
They discharge HEPA-filtered air across the work surface and toward the user.
-
These devices only provide product protection.
-
They can be used for certain clean activities, such as the dust-free assembly of sterile equipment or electronic devices.
-
Should never be used when handling cell culture materials or drug formulations, or when manipulating potentially infectious materials.
-
Workers can be exposed to materials being manipulated on the clean bench.
-
Horizontal laminar flow clean air benches should never be used as a substitute for a biological safety cabinet in research, biomedical or veterinary laboratories and/or applications.
This information comes from the Biosafety in Microbiological and Biomedical Laboratories (BMBL) (CDC/NIH publication): Appendix A - Primary Containment for Biohazards: Selection, Installation and Use of Biological Safety Cabinets:
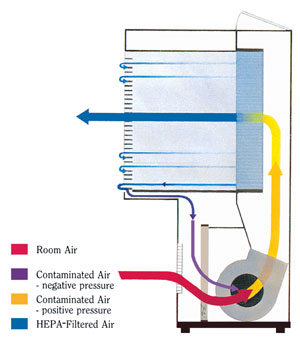
EHRS strongly discourages ANY use of Laminar Flow Clean Benches on campus.
-
Horizontal laminar flow clean benches are inappropriate for use with any potentially biohazardous material including human source material (clinical specimens, blood, tissue, etc.), cell cultures, infectious agents, or infected animal tissue.
-
Horizontal laminar flow clean benches are inappropriate for use with uninfected animals (lab animal allergy), hazardous chemicals and volatile radioisotopes.
-
Work with the above materials should be conducted in a Class II biosafety cabinet.
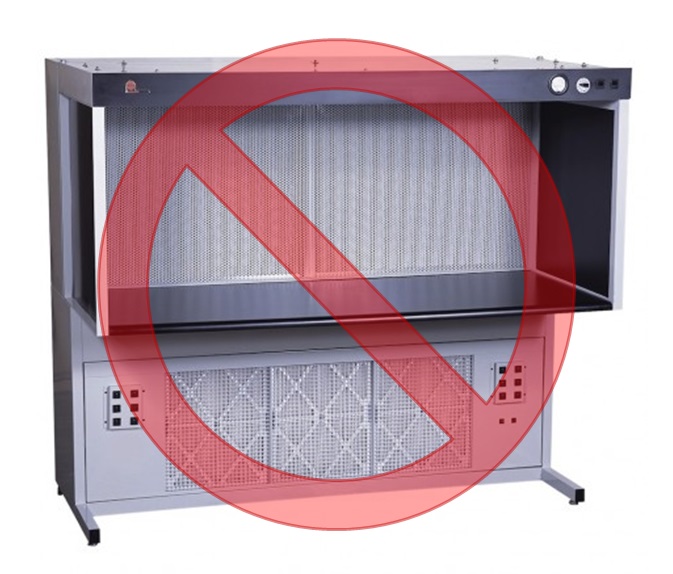
Vacuum Systems used with a Biosafety Cabinet should be protected with High Efficiency
Particulate Air (HEPA) filters, or their equivalent as stated in the CDC/NIH Guidelines for Biosafety Level 2 work. Filters must be replaced as needed. Liquid disinfectant traps may be required.
See the attached Quick Reference for additional guidance and suggested filters.
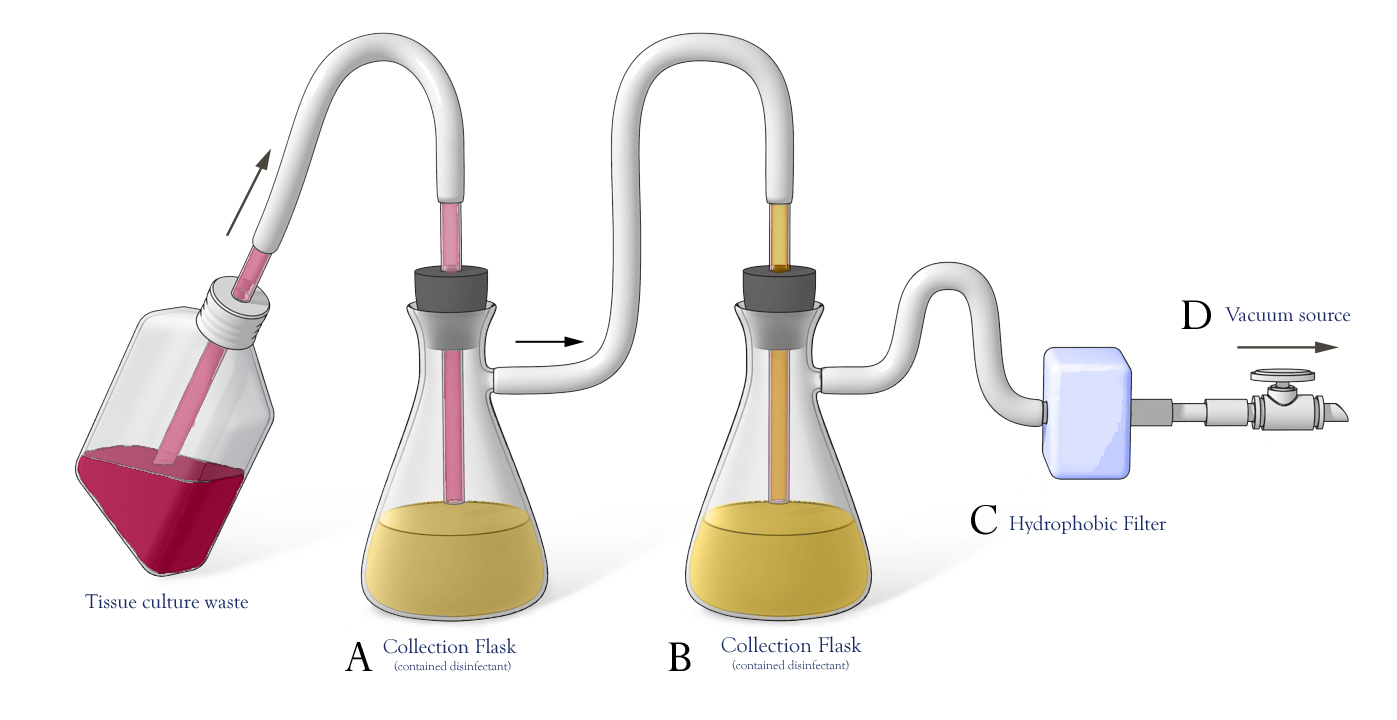